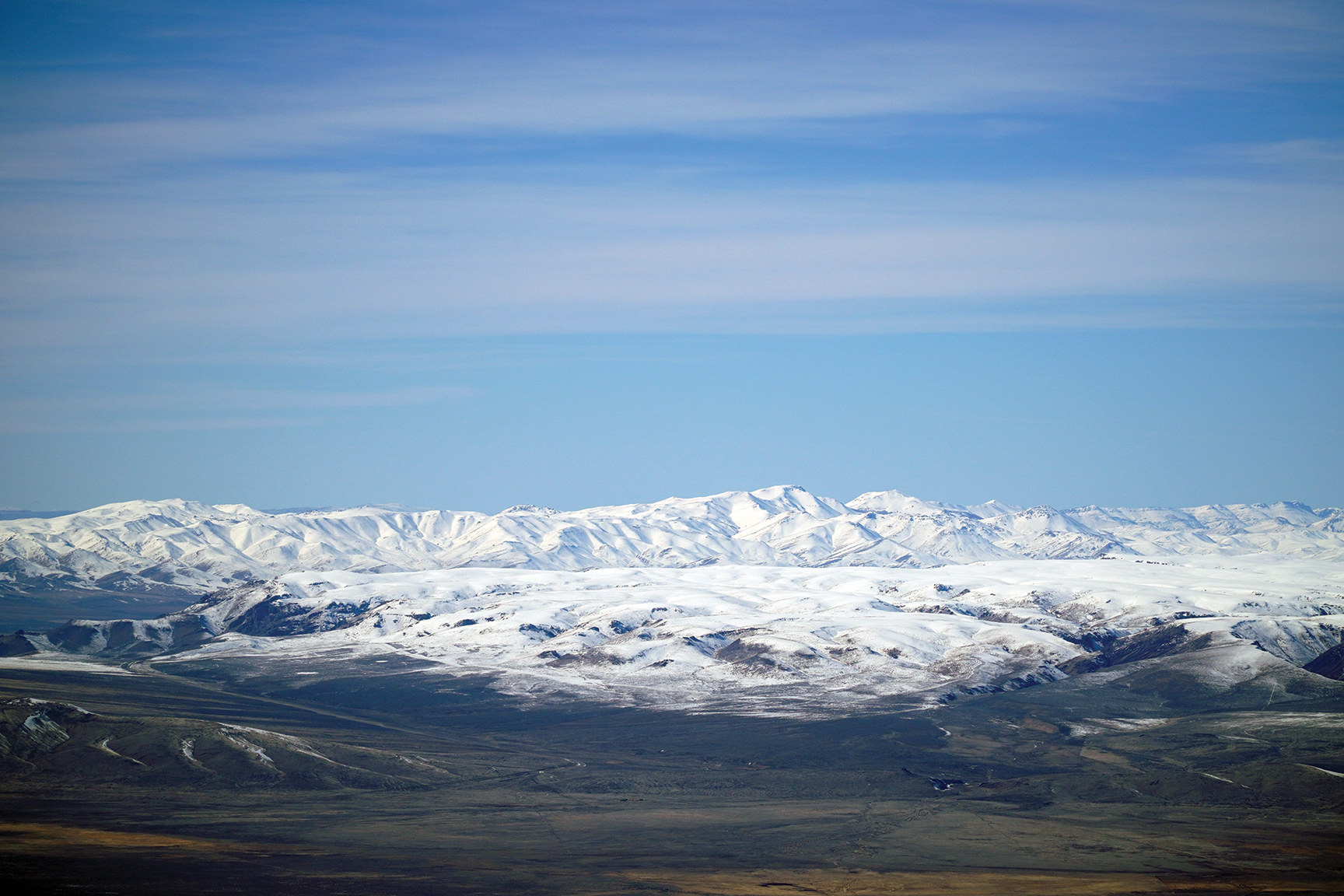
06 Dec Thacker Pass: The Crossroads of Lithium, Wild Snow and Sacred Land
Plans to construct one of the world’s largest open-pit lithium mines in Northern Nevada raise difficult questions about what local sacrifices must be made to support the global transition to clean energy
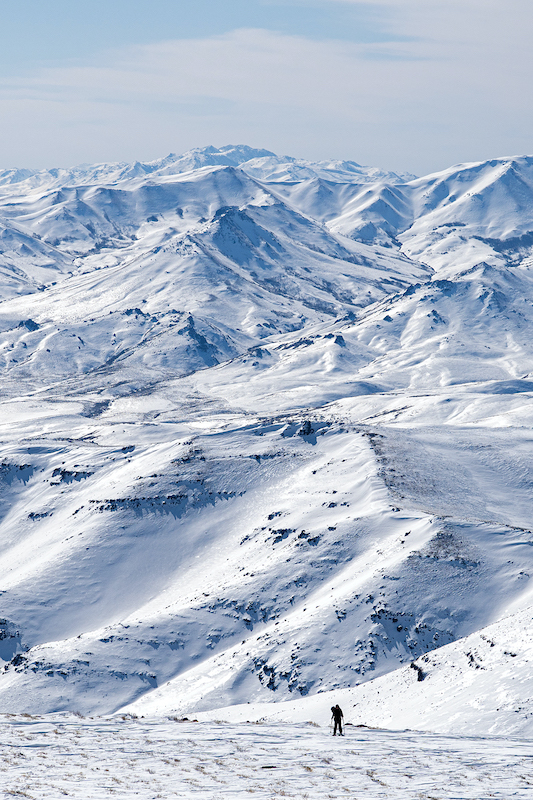
Allison Lightcap explores a little-known land of untold alpine beauty near Thacker Pass in March 2021. How air pollution from the mine might affect winter snowfall in these mountains is a concern of both local ranchers and winter recreationists, photo by Seth Lightcap
Local ranchers call it Thacker Pass. The native Paiute people call it Peehee Mu’huh.
We have no clue that this uninhabited expanse of desert land even has a name. It just looks like a good spot to pull the truck off the road for the night and get some sleep.
It’s a chilly evening in March 2021, and my wife Allison and I are three hours into a weekend road trip to go backcountry snowboarding in Northern Nevada. We drove from Lake Tahoe that afternoon, and are now 17 miles west of the tiny town of Orovada, Nevada, on the roughly paved Kings River Road.
We’re only a few miles from the trailhead, so it’s time to camp. Slowing our pace and flipping on the brights, we soon find a dirt spur road leading to a small, level clearing that checks all the boxes: The only lights we can see are stars, and the only sounds we can hear are coyote howls.
But little do we know, we are not alone. Somewhere out in the darkness along this same lonely stretch of two-lane road, there is another group of campers. They too have been drawn by the call of the desert wilderness, and the serene beauty of the sagebrush, but unlike us, they aren’t chasing powder turns, or any recreational pursuit, for that matter. This other group of campers is posted up in protest of a mining project.
Unbeknownst to us, we have stopped to camp on federally owned land that is the proposed site of a massive open-pit lithium mine known as the Thacker Pass Lithium Project. The mine is in development by Lithium Nevada, a company based in Reno that is a wholly owned subsidiary of a Canadian mining company named Lithium Americas. Lithium Nevada plans to make Thacker Pass a major domestic source of this elemental metal that is an essential ingredient in electric vehicle (EV) batteries and a critical resource in the global movement toward clean energy.
A vast majority of the worldwide lithium supply is mined in Australia, China and the Lithium Triangle of Argentina, Chile and Bolivia. The Thacker Pass mine would help alleviate the United States’ near total dependence on foreign sources of lithium, but the project is also expected to come with significant community and environmental costs.
The group of protesters we share our starry view with that evening, along with local Native American tribes, neighboring ranchers and environmental groups, are adamant that the mine will destroy sacred tribal land, use too much groundwater, upset threatened wildlife habitat and leave a gigantic pile of mining waste that may pollute the local water supply for centuries.
The Bureau of Land Management (BLM) published the Final Environmental Impact Statement (EIS) for the mine project in December 2021. The EIS downplays these concerns and makes the case that the mine will use “best available technologies” to avoid any environmental catastrophes. The Trump administration agreed with that assessment and on January 15, 2021, issued a Record of Decision that formally approved the federal permit for the mine.
Strong opposition to the project quickly followed, including multiple federal lawsuits contesting the findings of the EIS, and a permanently occupied protest camp on the mine site.
Allison and I know nothing of this contentious battle over Thacker Pass as we proceed with our weekend plans to climb and ride a few of the tallest peaks surrounding the pass. It isn’t until a couple of weeks after we return home from our snowboarding adventure that we come across news of the proposed mine.
The news shakes us to our core, but not because we are immediately opposed to the mine.
We are fervent wilderness advocates, so the notion of a mine desecrating a natural area we cherish makes our skin crawl, but we also believe that the rapid advancement of electric vehicles and renewable energy systems that require lithium are crucial to stopping global warming.
Our uncertainty about the costs versus benefits of the mine, and whether the local sacrifices it will demand are worth accepting in support of fighting climate change and creating local jobs, is deeply unsettling to us. Should we join the protesters or concede that the mine is a necessary evil?
Without a clear answer, and unfamiliar with the nuances of lithium mining, there was only one solution: Talk to the experts and dive into an attempt to understand the issue from all sides.
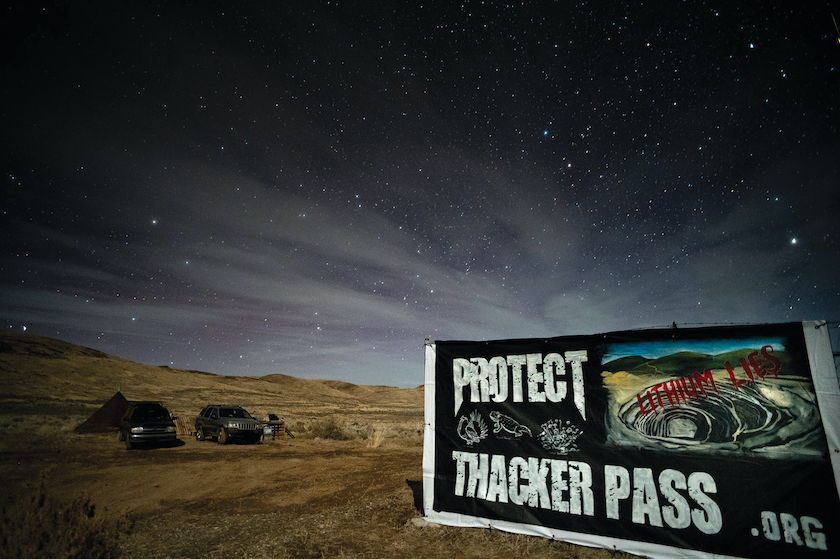
Environmental activists Max Wilbert and Will Falk established the Protect Thacker Pass protest camp on January 15, 2021, the same day the Trump administration approved the mine, photo courtesy Max Wilbert
Why Thacker Pass?
It’s not hard to grasp why we are in a race to develop new lithium mines in the United States. The International Energy Agency, an organization that tracks world energy usage, estimates that the global demand for lithium will increase more than tenfold by 2030, and potentially 50 times greater by 2040.
These aggressive projections have sparked a lithium gold rush, with the world’s superpowers racing to secure a domestic supply. The United States trails Australia, China and several other countries by a wide margin, as the only large-scale lithium mine currently operational in the U.S. is in Nevada’s Clayton Valley, which produces not even 2 percent of the current global supply.
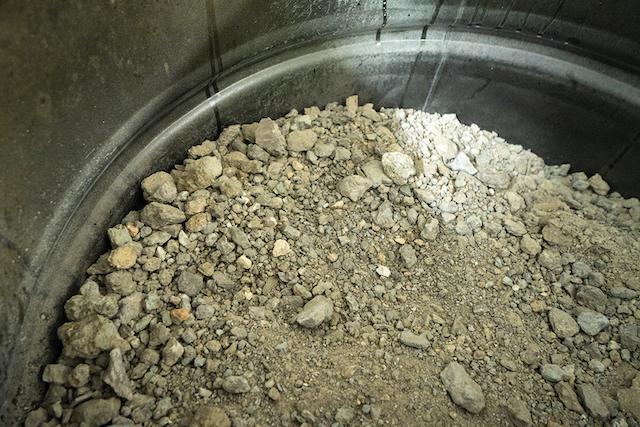
A barrel of “white gold”—lithium-rich claystone from Thacker Pass —awaits processing at Lithium Nevada’s research facility in Reno, photo by Seth Lightcap
Answering the call for increased domestic production, mining companies are working on new lithium projects in Arkansas, Tennessee, North Carolina, North Dakota, Maine, Oregon, Nevada and California. Other than location specifics, what differentiates all these projects is the concentration and host material where the lithium is found.
Lithium can be found in “hard rock,” brine and claystone deposits. Hard rock mines, such as those in Australia and a newly approved mine in North Carolina, dig and blast up lithium-rich minerals from an open pit. The lithium is then extracted from the rock using an energy-intensive, acid-based chemical process that creates a lot of waste. Hard rock mining is the dirtiest way to mine lithium, but the one upside is that it is the easiest way to produce lithium hydroxide, which is the preferred lithium compound for making high-performance and long-lasting EV batteries.
Lithium brine operations, such as those in South America and a pending project in California’s Salton Sea, pump lithium-rich groundwater into large collection ponds. The water slowly evaporates from the ponds, leaving behind a high concentration of lithium in the remaining solution. Brine operations are thought to be the most eco-friendly way to produce lithium because they use less chemicals and create less waste. The downsides of brine are that the process uses a lot of water and takes a long time. Most brine operations also produce lithium carbonate, which is a slightly lower-quality lithium compound that’s primarily used in laptop and cellphone batteries.
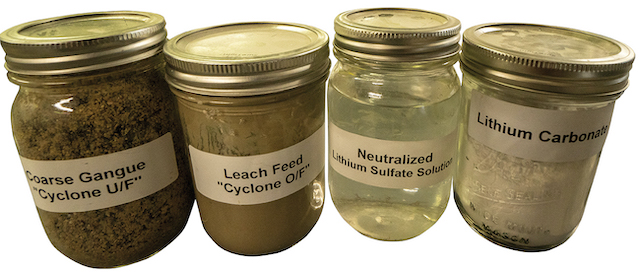
Sample jars of materials from different processing stages, including leach feed, which is the clay slurry that starts the process, and lithium carbonate, which is the end product that gets made into batteries, photo by Seth Lightcap
The Thacker Pass project would be the world’s first lithium claystone mine. The mine would use hydraulic shovels to dig up the soft claystone from an open pit and then extract the lithium from the clay with a newly developed extraction process. Claystone requires less energy to mine than hard rock, but the extraction does still require an acid-based chemical process that creates a lot of waste. Lithium Nevada’s plan is to produce lithium carbonate at Thacker Pass, but it may pivot to producing lithium hydroxide if the market demands.
The incentive to develop a pioneering claystone extraction process lies in the amount of lithium Thacker Pass holds. The pass is part of the McDermitt Caldera, an ancient volcanic hotspot that encompasses over 700 square miles in Nevada’s Humboldt County and southeastern Oregon. The caldera exploded 16 million years ago, after which a lake formed in the caldera. Vast amounts of lithium rose to the earth’s surface with the volcanic magma and then deposited in the sediments of the lakebed over the next several hundred thousand years. Tectonic uplift then pushed mountains up through the lakebed, leaving what is now thought to be the largest lithium clay deposit in the United States at the earth’s surface on Thacker Pass.
Lithium Nevada estimates there is 13.7 million tons of lithium on Thacker Pass, enough for a mine life of 46 years. The company plans to split the mine life into two phases. The first four years of mine operation would be phase one, during which an annual production of 40,000 tons is projected. The remainder of the mine life constitutes phase two, during which annual production would jump to 80,000 tons—almost a quarter of current global supply. The total amount of lithium produced globally in 2020 was 345,000 tons.
Block Mining and Backfilling
There is no doubt that Thacker Pass holds an impressive amount of lithium that could dramatically improve our country’s domestic lithium supply. But what’s in the ground is not what’s in debate. It’s Lithium Nevada’s plan for taking the lithium out of the ground that has local ranchers, environmental groups and native tribes up in arms.
The mine site is slated to occupy roughly 18,000 acres, with most of that land used for processing facilities and transportation logistics. Only 5,500 acres will be actively mined over the 46 years. Because the mine area is predominantly made up of soft clay, hydraulic shovels will be used to scoop up the ore and dump it into 100-ton mining trucks that will then deliver it to the first processing stage.
“We have a very soft and shallow deposit that presents a lot of benefits,” says Tim Crowley, vice president of government affairs and community relations for Lithium Nevada. “We won’t need to do much blasting, and we’re only going to mine down to 400 feet, which is really shallow in mining terms. There is no reason to dig deeper because that’s where we hit the ancient lake bottom, and there’s no lithium below that. It’s going to be simple truck-and-shovel mining.”
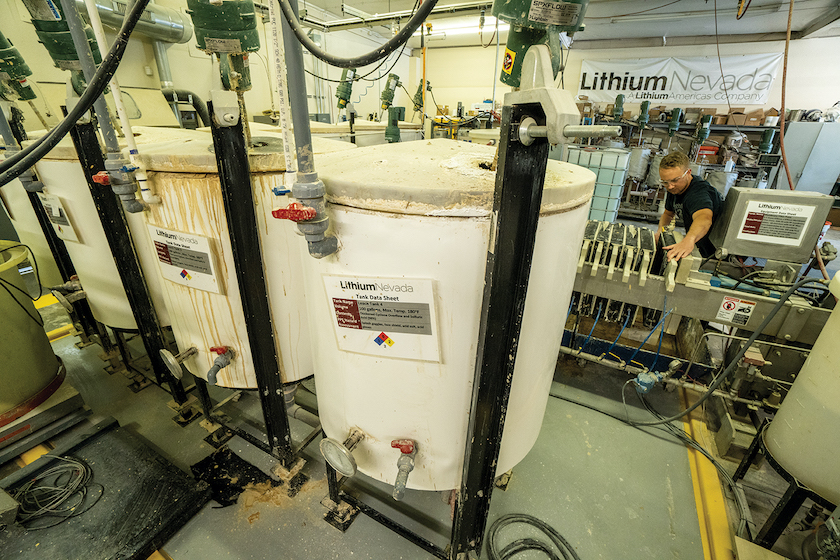
The facility tests the newly developed sulfuric acid-based lithium extraction process that the mine would use, photo by Seth Lightcap
Lithium Nevada won’t be doing the digging, however. The company has partnered with Sawtooth Mining LLC, which has experience mining soft minerals to handle all mining and reclamation operations. Lithium Nevada will take over processing once the ore is out of the ground.
The ore will be excavated using a block-mining technique that continuously backfills the pit throughout the life of the mine.
“The beauty of block mining is that our pit will never grow to be a 5,000-acre opening,” says Crowley. “The pit will never be more than 1,000 acres, because as we move laterally, we will put the waste rock back in the hole. At the end of the mine life, the pit will already be almost completely backfilled.”
Waste rock is the material that doesn’t contain enough lithium to be processed. Because the area is so highly mineralized, the waste rock will likely contain elevated levels of hazardous minerals like arsenic and antimony. To stop these pollutants from leaching into the groundwater, the bottom of the backfilled areas will be lined with a layer of hard inert clay.
In year 20 of the mine plan, digging would commence in an area where the lithium-rich clay dips below the water table. To avoid contaminating the groundwater will then require a different containment method that has yet to be decided or approved.
The Nevada Department of Environmental Protection (NDEP), the state agency tasked with monitoring industrial emissions, gave preliminary approval to Lithium Nevada’s water pollution control plans in October 2021, but the conditional permit it issued restricts the mine from digging deeper than 15 feet above the water table. Lithium Nevada expects that additional studies on the water flows around the pit conducted over the next decade will allow them to find a safe solution for mining below the water table.
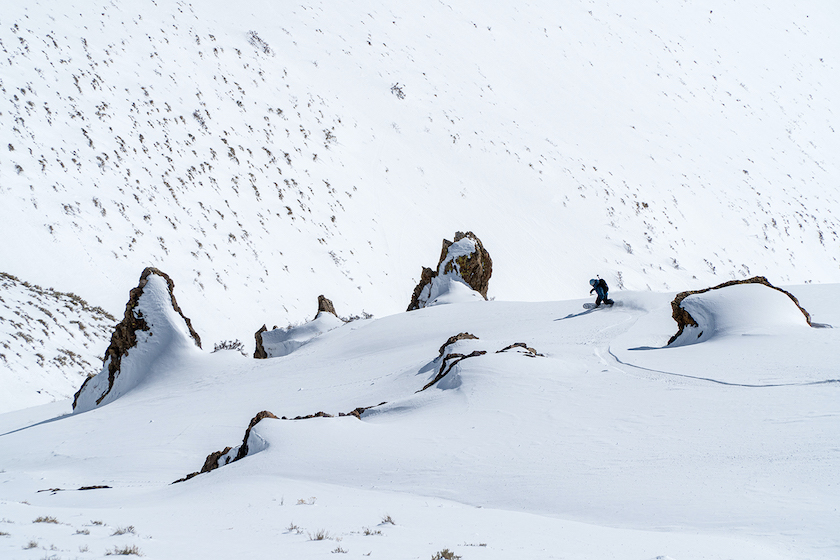
Allison Lightcap carves into a shallow Northern Nevada snowpack in March 2021. A succession of below-average winters throughout the last decade have plunged most of Nevada into a severe drought and made the mine’s proposed water usage worrisome, photo by Seth Lightcap
Worries About Water
Once the clay is out of the ground, Lithium Nevada’s newly developed extraction process begins. To perfect this process before building the large-scale mine facilities, the company opened a small-scale research facility in Reno, where it has been processing samples of Thacker Pass clay for the past two years.
The first step in processing the clay is to mix it with water and create a slurry. The slurry is then agitated to break out the non-lithium-containing sand and rock. The sand and rock get immediately dumped back in the pit and the milkshake-consistency slurry gets pumped on to the first processing plant.
In phase one, the mine will use 2,600 acre feet a year, or approximately 847 million gallons of water, to make the lithium slurry. In phase two, water usage will double to 5,200 acre feet, or approximately 1.7 billion gallons a year. In either phase, 27,000 gallons of water will be used to produce one ton of lithium.
The mine’s water usage is worrisome for local ranchers because water rights are already over-allocated in the Quinn River watershed, according to the BLM.
Lithium Nevada has secured water rights to cover its phase one usage by purchasing a ranch in the Quinn River Valley, plus water rights from another local rancher. To avoid having to pipe water from those properties, Lithium Nevada has also applied for a point of diversion permit that, if approved, will allow the company to draw its allocated water from wells closer to the mine site.
Changing the location of the water draw is one of the primary concerns of Edward Bartell, a Quinn River Valley rancher who filed a federal lawsuit in February 2021 contesting the findings of the EIS. Bartell owns a cattle ranch adjacent to the mine site that includes an 800-acre stand of naturally occurring ryegrass that he uses to graze his livestock.
“The vegetation on our land relies on the relatively high water table. If the mine draws down the water table too far, it will turn our private land into barren desert, and be devastating to our livelihood,” says Bartell.
According to the EIS, phase two is expected to draw down the water table by up to 10 feet for over a mile radius surrounding the mine’s two wells. The mine’s primary well will be in the Quinn River Valley near three of Bartell’s wells, and the water will get pumped 5 miles up to the pass in underground piping.
The EIS admits that the mine’s water draw will drop the level of Bartell’s wells, but claims that it should not dry up his land. Bartell contests that analysis and believes the EIS results were calculated using inaccurate baseline water table data collected by an assessor who was biased toward the BLM and overestimated the amount of water in the watershed.
Lithium Nevada has countered Bartell’s claims, saying that it has monitored how its water usage will affect the water table for over 10 years using monitoring wells.
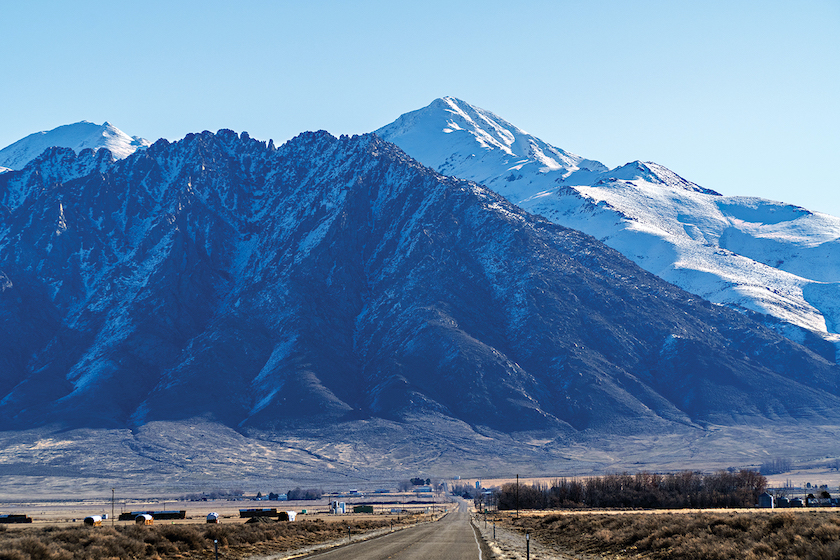
To keep up with the sulfur and material needs of the mine, between 120 and 200 semitrucks a day would drive this roughly paved stretch of Kings River Road leading out of the town of Orovada, Nevada, photo by Seth Lightcap
Serious Concerns About Sulfur
Once the lithium clay is mixed with water to form the slurry, it is then pumped to a processing plant where the slurry is mixed with sulfuric acid. The sulfuric acid leaches the lithium from the liquefied clay and suspends it in its elemental state within the solution.
While sulfuric acid is a commonly used industrial chemical, the use of it in Lithium Nevada’s extraction process is also contentious because of how much is needed and how it will be produced.
Sulfuric acid can be transported by truck, but it’s very dangerous if spilled. So the mine plans include an onsite sulfuric acid manufacturing plant. The sulfuric acid will be made by burning molten sulfur that’s brought in by the truckload from Winnemucca.
“The upsides of making our own sulfuric acid are tremendous,” says Crowley. “For one, the chemical reaction going from sulfur to sulfuric acid creates heat, which we will use to produce carbon-free power that will be the primary energy source for the processing plant. The other upside is that we’ll only need to truck in a third of the material. So we eliminate two-thirds of the truckloads by making sulfuric acid on-site.”
In phase two of mine operations, the sulfuric acid plant will produce 5,800 tons of sulfuric acid a day. To produce that much sulfuric acid will require burning approximately 1,900 tons of sulfur a day, which is roughly 75 semitruck loads. Between the delivery of sulfur and other necessary materials for mine operations, the EIS states that 120 to 200 semitrucks will make the 60-mile drive from Winnemucca to the mine every day and arrive at any hour.
Bartell is appalled by the amount of sulfur that will be trucked in and from where it will be sourced.
“They will need to import 800,000 tons of sulfur annually to create only 80,000 tons of lithium. So we’re talking about a 10-to-1 waste ratio,” says Bartell. “They also intend to obtain the sulfur from oil refineries, and the very reason the refineries have cheap sulfur to sell is because they remove it from fuel because it causes pollution when we burn it in our cars.”
Burning sulfur creates sulfur dioxide, which is a toxic gas that contributes to global warming. The sulfur dioxide will account for a portion of the 152,703 tons of carbon emissions that mine operations will emit annually—the equivalent of a small city.
Most of the carbon emissions will come from the tailpipes of mining vehicles and supply trucks. To control emissions from the sulfuric acid plant and the clay processing plant, Lithium Nevada says it is committed to installing an air pollution control system that meets all state regulations. The NDEP is satisfied with Lithium Nevada’s air pollution control plans and gave the company preliminary approval by issuing a draft Class II Air Permit in October 2021.
Reclamation and Habitat Restoration
After treatment with sulfuric acid, the slurry is pumped to a final processing plant, where it’s pushed through filter presses that separate the lithium solution from the clay. The elemental lithium solution then gets transformed into lithium carbonate or lithium hydroxide, which are the materials that can be made into batteries.
The relatively dry and neutralized leftover clay tailings are then placed in a lined containment facility inside the pit using a “dry stack” method that compresses the tailings to minimize water runoff.
Glenn Miller, a professor emeritus at University of Nevada, Reno, who has been a critic of the mining industry in Nevada for the past 40 years, is impressed with Lithium Nevada’s plan to contain the tailings compared to many of the gold mines he has worked with in Nevada.
“Tailing facilities are always a problem, but in this case the tailings are mainly neutral material, and even if the tailing piles do leak, the primary chemical runoff will be sulfate, which is a very commonly used agricultural amendment in our region,” says Miller.
Despite stopping several mines in his career, Miller fully supports the Thacker Pass mine.
“Overall, it’s a question of how important this resource is,” says Miller. “If this was a gold mine, I would not be supporting it. But this is a lithium mine, and it does not have the problems that a gold mine of this size does. By comparison, it’s a relatively benign mine, and it’s producing something that is critically important to mitigating climate change.”
Miller’s support for the mine conflicts with the opinion of the Great Basin Resource Watch (GBRW), an environmental group based in Reno that Miller helped found in 1994, but is no longer affiliated with. The GBRW, along with three other environmental watchdog groups, filed a federal lawsuit contesting the EIS and the fast-tracked permitting process in February 2021.
“The mine went through the federal permitting process in just under a year, which was extremely fast for a large and complex mine proposal in a new area,” says John Hadder, executive director of the GBRW. “That was way too fast. And as a result, a lot of concerns were not addressed. One of which is the cultural significance of the area to the local indigenous communities, along with issues surrounding wildlife and sage grouse migration corridors.”
Thacker Pass is used as a migration corridor for pronghorn antelope and a nesting area for golden eagles and greater sage grouse, a threatened bird native to the Great Basin. The Nevada Department of Wildlife has found that habitat destruction is the primary threat to sage grouse, and notes that noise alone from the mine project may cause a known population of sage grouse located less than a mile from the mine site to abandon their habitat.
In the EIS, the BLM acknowledges the risk to sage grouse habitat, but suggests the mine will not be as disruptive to their habitat as recent fires in nearby sagebrush lands. Lithium Nevada has proactively worked with University of Nevada, Reno on sagebrush restoration. The company helped establish the Great Basin Sagebrush Restoration Fund, which supports the university’s research on new ways to reseed and restore stands of sagebrush destroyed by fire.
Mixed Signals on Sacred Land
In 2010, while creating a district-wide Resource Management Plan, the BLM Winnemucca office contacted all the federally recognized native tribes in Northern Nevada and Southeastern Oregon for consultation on where their tribes’ sacred and culturally sensitive sites were located. In response, the Fort McDermitt Paiute-Shoshone Tribe, whose tribal lands are less than 40 miles north of Thacker Pass, requested to be consulted about any pending projects on the pass, but did not identify the land as a sacred site. All the other consulted tribes deferred judgment on the cultural value of Thacker Pass to tribes that lived closer to the pass.
During the EIS preparation process, the BLM contacted the Fort McDermitt tribe in 2018 and 2019 regarding the potential cultural significance of Thacker Pass. The tribe did not raise any concerns about the mine. The EIS also required that an inventory of all cultural resources within the mine project area be documented. Subcontracted archaeologists completed the assessment by walking every acre of the mine site. The only prehistoric artifacts found were rock chips associated with obsidian toolmaking and grinding implements.
Fast forward to July 2021, and the Reno-Sparks Indian Colony, the Burns Paiute Tribe, plus a group of Fort McDermitt Tribe members identifying as Atsa koodakuh wyh Nuwu (People of Red Mountain) filed a legal challenge in federal court alleging that the BLM violated the National Historic Preservation Act because it did not adequately consult the tribes before permitting the mine. The challenge sought to halt an additional cultural assessment that would require digging shallow trenches with a backhoe at several locations on the mine site.
The legal challenge said new evidence suggesting a massacre of 31 Paiute people by the Nevada Calvary that occurred within the mine site in September 1865 had changed the tribes’ view on the cultural value of the land.
In September 2021, federal judge Miranda Du, who is presiding over all the pending legal challenges to the mine, denied the tribes’ challenge, citing BLM documentation detailing adequate consultation with the tribes, and vague evidence about the exact location of the massacre.
The Fort McDermitt Tribe, many of whom are descendants of the one adult male who survived the massacre, was not a plaintiff in the legal challenge because the tribe is divided over support for the mine. In March 2021, a majority of the 340 Fort McDermitt Tribe members signed a petition asking the tribal council to withdraw from a community engagement agreement with the mine. Many tribe members feel the mine will be a desecration of sacred land, while others look forward to the high-paying steady jobs the mine will bring to the area.
The mine is expected to bring 1,000 jobs during the construction phase and 300 permanent jobs once operational. Over 40 Fort McDermitt Tribe members have participated in Lithium Nevada’s initial job training events in hopes of securing one of the permanent mine jobs, which would pay between $60,000 and $90,000 a year.
Lithium Nevada is also attracting support from some Fort McDermitt Tribe members and residents of the neighboring town of Orovada with its commitment to build a new school in Orovada if the mine is approved.
The current schoolhouse is located on the road that will be used by the mine’s never-ending truck traffic and is in serious disrepair. Lithium Nevada presented plans to the Orovada community in June 2021 for a $12 million dollar school and community center on a new 30-acre parcel that includes a STEM lab, art/music room, detached gymnasium, track, basketball court and rock-climbing wall.
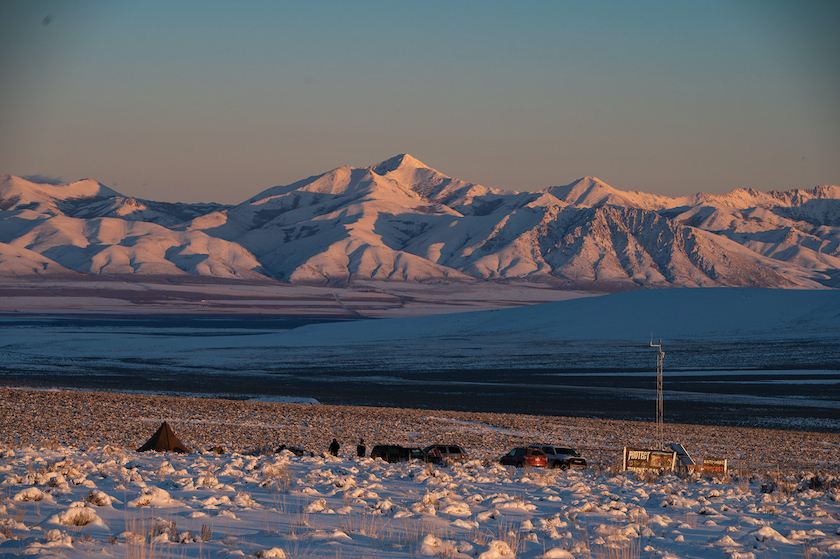
Alpenglow lights up the Santa Rosa Range and the protest camp in February 2021. The camp occupies a small clearing in the sagebrush next to a weather station on the proposed mine site, photo courtesy Max Wilbert
Standing Their Ground
Max Wilbert and Will Falk are the environmental activists who set up the protest camp on Thacker Pass. They pitched their tents for the first night of occupation on January 15, 2021, the same day the Trump administration approved the mine. Falk is also a lawyer, which has allowed the “Protect Thacker Pass” movement the pair founded to provide legal support to the tribal organizations who have recently mounted challenges to the mine.
“I knew this part of Nevada was exceptionally special, and that it didn’t get a lot of love,” says Wilbert. “If a massive open-pit mine was proposed in the middle of the redwood forest or a wetland on the Mississippi Delta, you could find a lot of people ready to fight it, but so few people have any experience with this land, I knew that maybe no one was going to stand up and take direct action for it.”
For the first couple of weeks of the protest, Wilbert and Falk were indeed alone on Thacker Pass. But after getting the word out about their cause through press releases, blog posts and social media, they found support flooding in from around the globe—and just up the road.
Fort McDermitt Tribe members who oppose the mine soon joined the camp, while Wilbert and Falk helped them organize their efforts to fight the mine.
“This is traditional land that was stolen from them,” says Wilbert. “We can’t change what happened in the past, but we can change our actions in the present, and help native people stand up to the destruction of their traditional lands moving forward.”
Wilbert estimates nearly a thousand people came to visit the protest camp during the summer of 2021. At many of the camp gatherings, native elders from the People of Red Mountain and other local tribes hosted ceremonies and prayer circles.
With canvas tents and a wood-burning stove, the protest camp is prepared to occupy the mine site through the winter.
“We are under no illusions. We know we are up against very powerful forces, but if you don’t fight, you are guaranteed to lose,” says Wilbert. “For me, the choice is between sitting at home and watching corporations destroy the planet or taking action and trying to do something about it.”
Wilbert and Falk are both experienced direct-action protesters and have suggested that the Protect Thacker Pass movement is prepared to put their bodies on the line in non-violent protest if plans for the mine move forward.
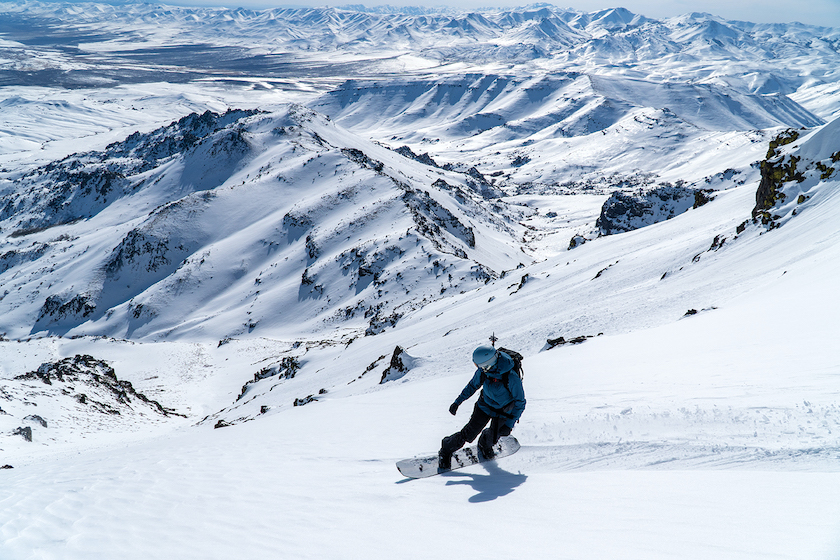
From volcanic hot spot to cool shred spot: Allison Lightcap drops into a dreamy backcountry descent on the boundary of the McDermitt Caldera, photo by Seth Lightcap
More Questions than Answers
Whether protesters must chain themselves to bulldozers to block construction on the mine won’t be decided for several more months.
Judge Du has said in previous rulings that she intends to hear the challenges to the EIS and make a ruling on the merits of the entire case in the first quarter of 2022. But there is a lawsuit winding through the state court system as well, and the potential for additional legal challenges that could further delay any binding decision on the mine.
With snow already on the ground at Thacker Pass, Lithium Nevada’s contested archeological excavations will also have to wait until the spring.
While waiting for his time in court next year, Bartell hopes the lithium industry keeps making technological leaps and bounds that prove Thacker Pass is the wrong place to mine.
“This is evolving technology, and rather than stampeding ahead with a mine that will likely result in enormous amounts of pollution, we should be looking at new ways of extracting lithium that are much cleaner and have a better chance of becoming carbon-neutral than Thacker Pass. Supposedly clean-energy solutions that actually cause pollution defeat the purpose of creating clean energy,” says Bartell.
Miller, on the other hand, is not holding his breath for new technology. He feels there is no time to waste.
“If there is a new lithium extraction technology that can be made scalable and price-competitive in the United States, that’s great, but we aren’t there yet,” says Miller. “Some feel we should wait a few years to see if a new technology will come online, but I argue, I don’t think so. Climate change is staring us in the face and we need more lithium to fight it as soon as we can get it.”
Circling back to how Allison and I stumbled upon the Thacker Pass project in the first place, as two backcountry snowboarders who love exploring the mountains of Northern Nevada, we also wonder how a large increase in greenhouse gas emissions will affect the snowpack near the mine. Several recent studies by Colorado State University suggest that increased pollution levels can decrease snowfall and rainfall in mountain regions located near pollution sources.
So many questions, and so few answers, which brings up maybe the most important question of all about the mine project.
Lithium Americas presents a solution to just about every concern about the mine project, but it is a publicly traded company, whose largest shareholder is China’s Ganfeng Lithium, the largest lithium mining company in the world. Can Lithium Americas be trusted to put the health of the land, water and local community ahead of its bottom line and foreign shareholders?
True to Nevada, the fate of Thacker Pass is shaping up to be a high-stakes gamble that the local environment and community may pay dearly for in the global race for clean energy.
Seth Lightcap is an Olympic Valley-based writer and photographer who is continually blown away by the raw natural beauty of Nevada. See more of his stories at www.sethlightcap.com.
John Hadder
Posted at 11:29h, 20 DecemberMy name is John Hadder and I am the director of Great Basin Resource Watch (GBRW), our organization has been working with directly affected communities to protect their land, air, water, and culture from the negative affects of mining. In my 15 years of work with this organization the Thacker Pass EIS (federal permit process) was one of the worst I have seen, with many aspects of the mine unclear especially when it comes to mitigation of environmental impacts. The EIS also failed to fully delineate the cultural important of the area to the indigenous Pauite and Shoshone peoples. My organization was thus compelled to file against the EIS in federal court with Western Watersheds Project, Basin and Range Watch, and Wildlands Defense. Our perspectives and comments on the mine can found on our website – https://gbrw.org/proposed-thacker-pass-lithium-mine/ and https://gbrw.org/publications/.
Also the statement from Glenn Miller, “Tailing facilities are always a problem, but in this case the tailings are mainly neutral material, and even if the tailing piles do leak, the primary chemical runoff will be sulfate, which is a very commonly used agricultural amendment in our region,” says Miller. is incorrect. In documentation sent to the Nevada Division of Environmental Protection (NDEP), the state of Nevada permitting agency, it is clear that the tailings are in fact mostly acidic and not neutral. The tailings will have three components, leached filter cake ( LFilterCake), neutralized filtercake, and Salt. The percent breakdown is: “The tailings with salt samples were reconstituted at a ratio of 64.1 percent LFilterCake, 17.3 percent NFilterCake, and 18.6 percent Salt, as measured by dry weight.” (Technical Memorandum (385-TM-07-CTFS) Thacker Pass Project Tailings Assessment, NewFields Job No. 475.0385.000, December 20, 2019), where the 64.1 percent LFilterCake is acidic as stated in a May 26, 2021 document (Technical Memorandum, Summary of Baseline Geochemical Characterization for the Thacker Pass Project, SRK, May 26 2021), “The initial low pH [high acidity, i,d,] of the clay tailings sample (HC-17) is linked to the presence of residual sulfuric acid…” Thus, it is the leached filtered tailings that are acidic and are expected to constitute 64.1 percent of tailings generally, and what is true is opposite to what Miller stated. These documents can be obtained from NDEP, Bureau of Mining Regulation and Reclamation.
The acidic tailings is a significant environmental concern and GBRW is still trying assessment the ultimate risk and danger to the environment of the proposed tailings facility. Even though the state is requiring a heavy duty liner for the tailing facility, there still could be contamination. The tailings facility for Thacker Pass will be a first of its kind, so there is no field experience. Therefore, a detailed and through examination and assessment of the potential for water pollution is necessary, which in our view has yet to be done.
Simon
Posted at 02:01h, 30 JanuaryExcellent article on the complicated and contrary issues of going green and protecting the environment. Which and whose environment and just what are the opportunity costs, and who pays?
Thacker Pass and Kings River valley: some of the most underrated landscapes in the US. My favourite bit of Nevada.